Tu CPU viene de la arena
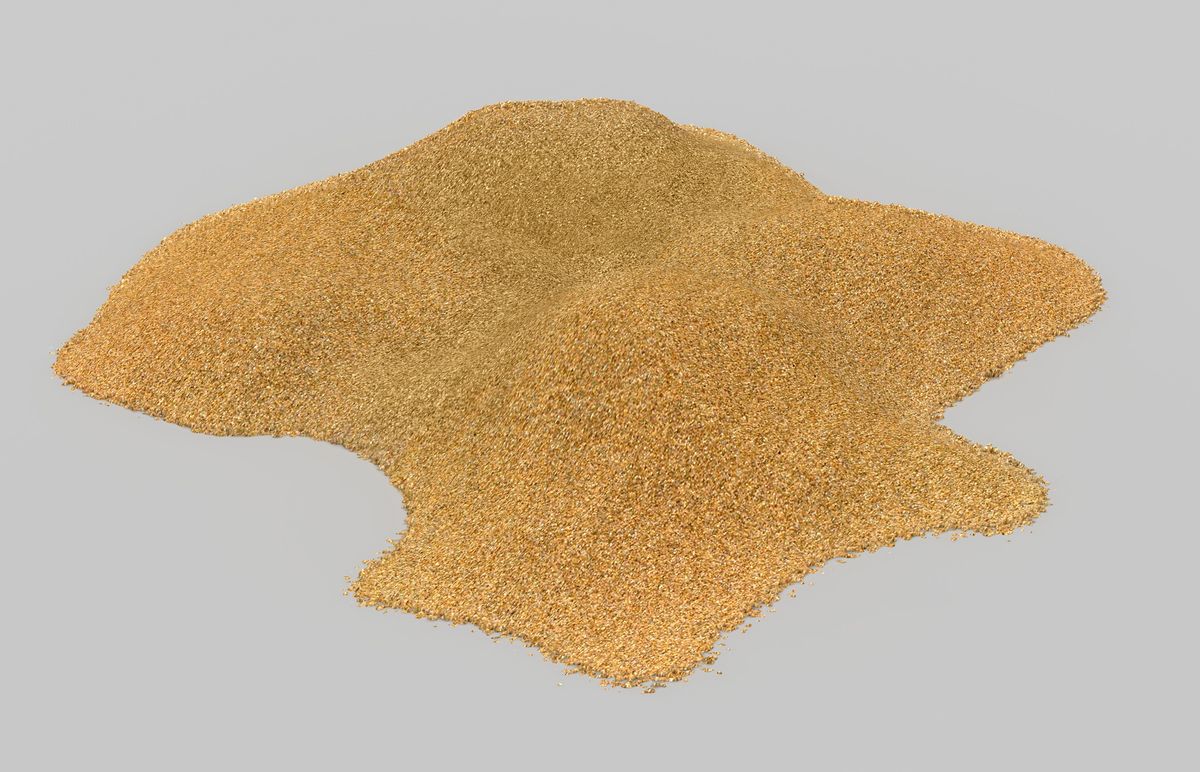
La arena. Compuesta por un 25 por ciento de silicio, es, después del oxígeno, el segundo elemento químico más abundante que hay en la corteza terrestre. La arena, especialmente el cuarzo, tiene altos porcentajes de silicio en forma de dióxido de silicio (SiO2) y es el ingrediente base para la fabricación de semiconductores.
Purificación y cultivo
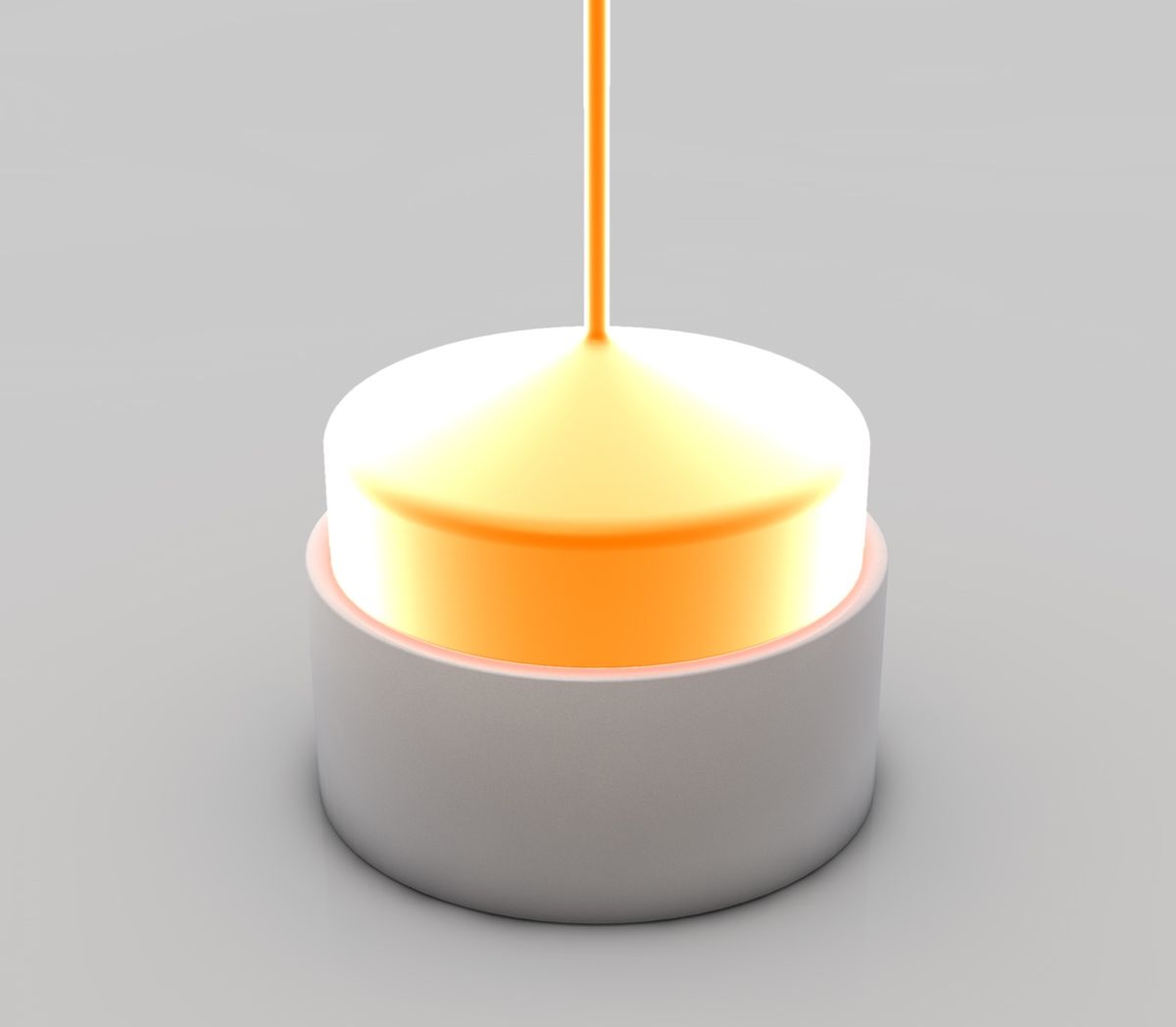
Después de obtener la arena bruta y separar el silicio, el material sobrante se elimina y el silicio se purifica en múltiples pasos para alcanzar finalmente la calidad de fabricación de semiconductores que se denomina silicio de grado electrónico. La pureza resultante es tan grande que el silicio de grado electrónico sólo puede tener un átomo extraño por cada mil millones de átomos de silicio. Tras el proceso de purificación, el silicio entra en la fase de fusión. En esta imagen se puede ver cómo crece un gran cristal a partir del silicio fundido purificado. El monocristal resultante se llama lingote.
Un gran lingote
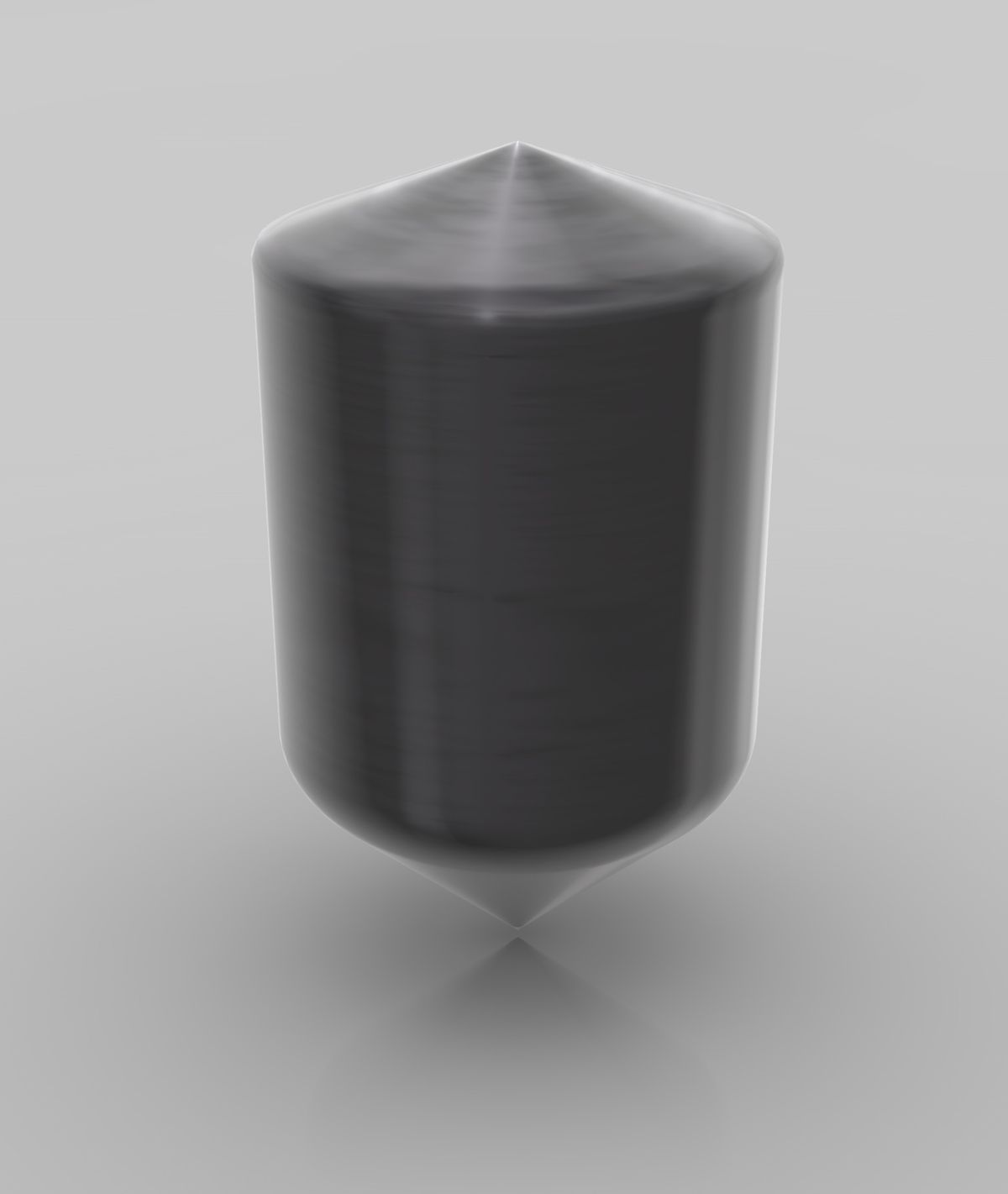
Un lingote monocristalino se produce a partir de silicio de grado electrónico. Un lingote pesa aproximadamente 100 kilogramos (o 220 libras) y tiene una pureza de silicio del 99,9999 por ciento.
Corte del lingote
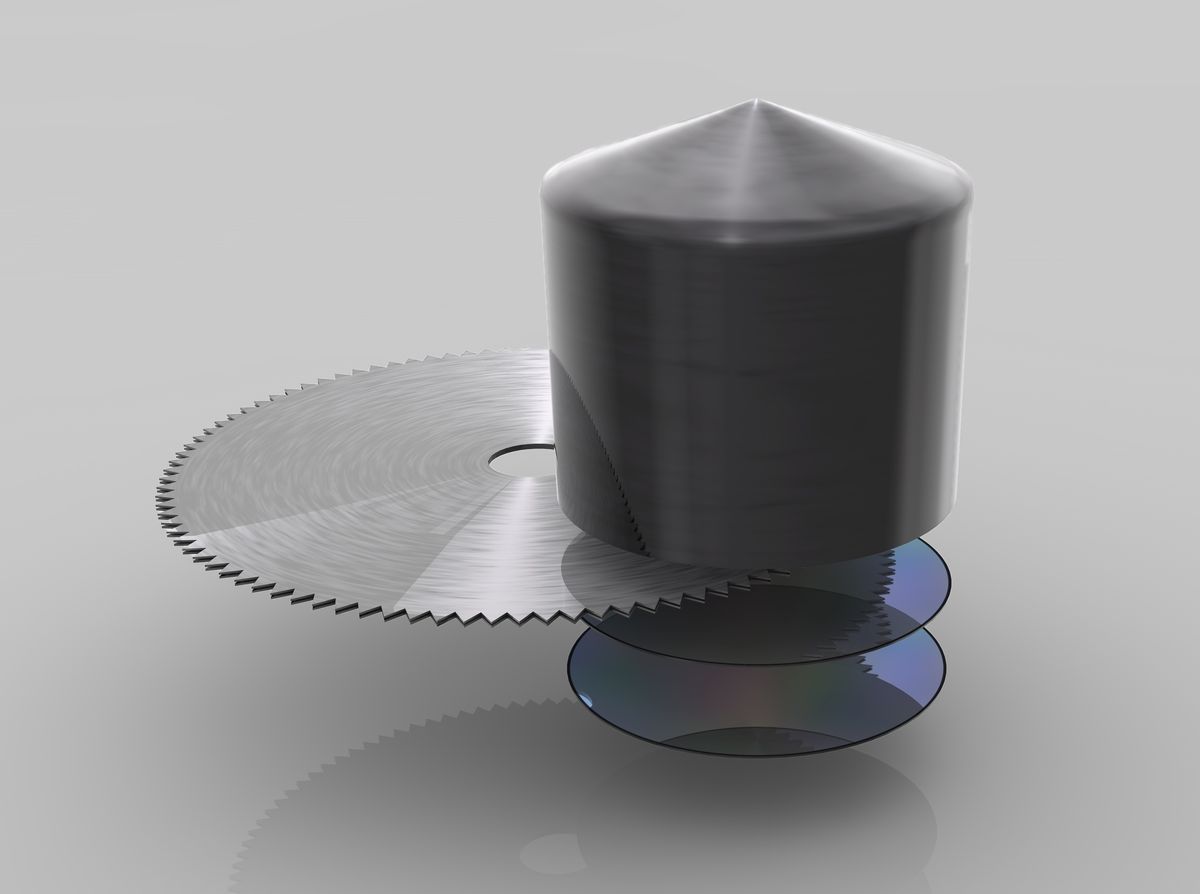
El lingote pasa a la fase de corte, en la que los discos de silicio individuales, llamados obleas, se cortan en rodajas finas. Algunos lingotes pueden superar el metro y medio de altura. Existen diferentes diámetros de lingotes en función del tamaño de la oblea requerida. Hoy en día, las CPU se fabrican normalmente en obleas de 300 mm.
Pulido de obleas
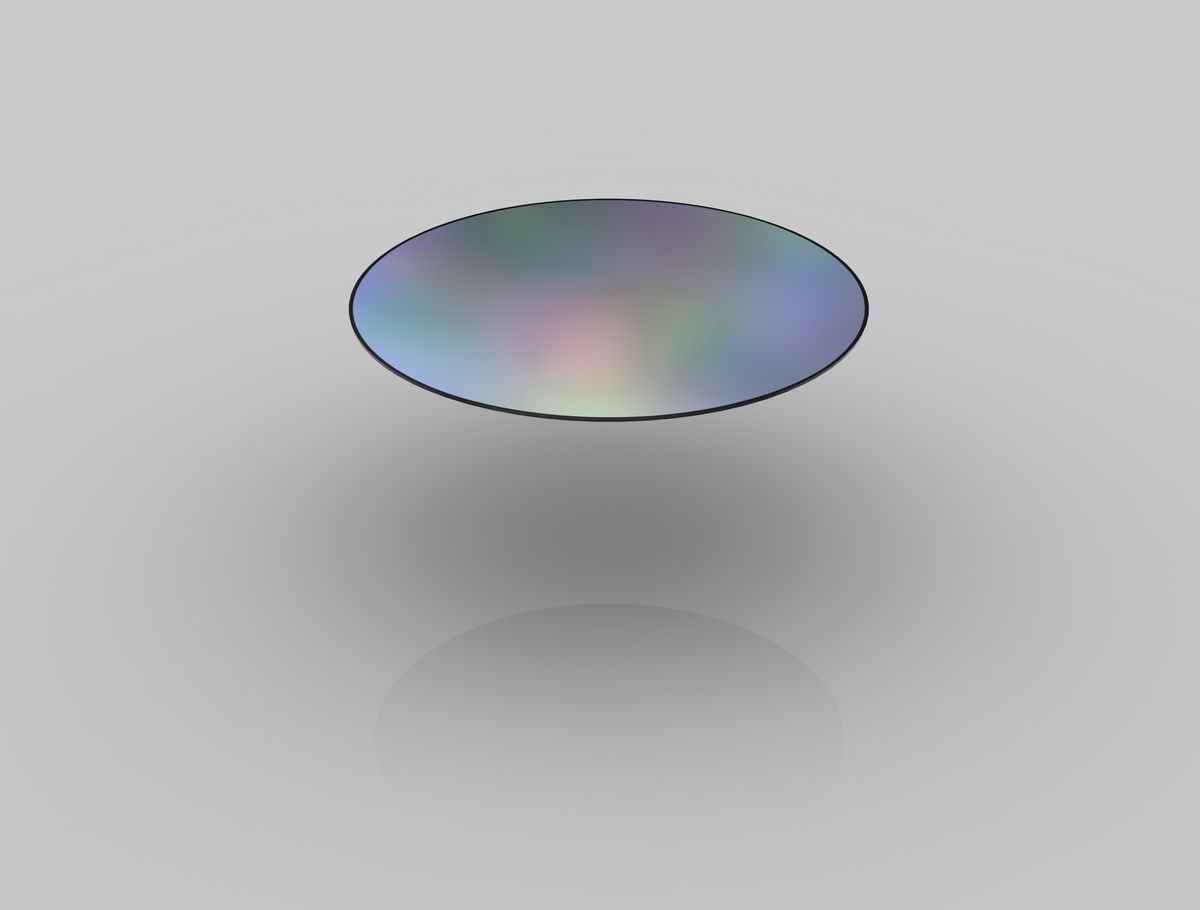
Una vez cortadas, las obleas se pulen hasta que tienen superficies impecables y lisas como un espejo. Intel no produce sus propios lingotes y obleas, sino que adquiere obleas listas para la fabricación a terceros. El proceso avanzado de 45 nm High-K/Metal Gate utiliza obleas con un diámetro de 300 mm (o 12 pulgadas). Cuando Intel empezó a fabricar chips, imprimía los circuitos en obleas de 50 mm (2 pulgadas). Hoy en día, Intel utiliza obleas de 300 mm, lo que se traduce en una disminución de los costes por chip.
Aplicación de fotorresistencia
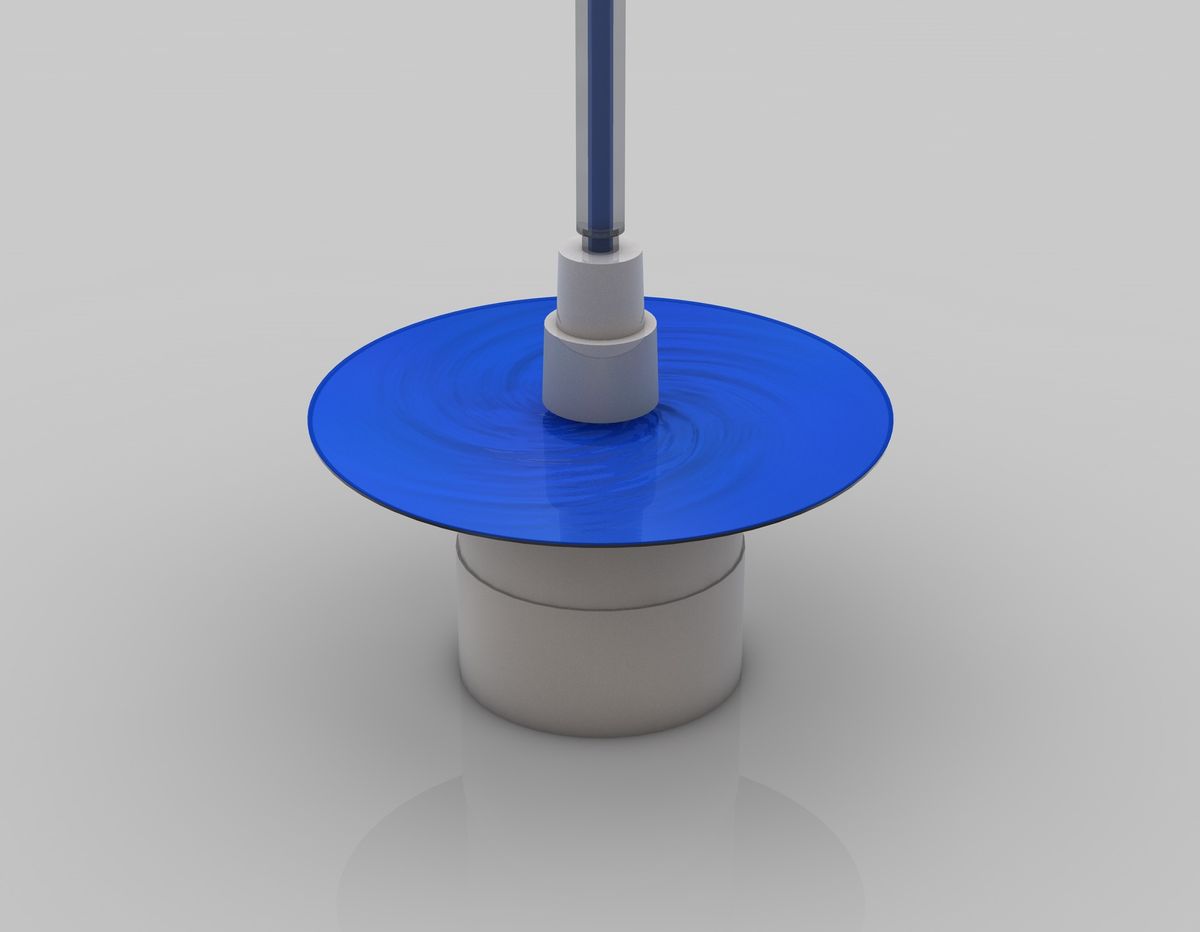
El líquido azul, representado arriba, es un acabado de fotorresistencia similar a los utilizados en las películas para fotografía. La oblea gira durante este paso para permitir una capa uniformemente distribuida que es suave y también muy fina.
Exposición a la luz UV

En esta etapa, el acabado fotorresistente se expone a la luz ultravioleta (UV). La reacción química desencadenada por la luz ultravioleta es similar a la que se produce en el material de la película de una cámara en el momento en que se pulsa el botón del obturador.
Las zonas de la resistencia en la oblea que han sido expuestas a la luz ultravioleta se volverán solubles. La exposición se realiza mediante máscaras que actúan como plantillas. Cuando se utilizan con luz UV, las máscaras crean los distintos patrones de los circuitos. La construcción de una CPU repite esencialmente este proceso una y otra vez hasta que se apilan múltiples capas unas sobre otras.
Una lente (en el centro) reduce la imagen de la máscara a un pequeño punto focal. La «huella» resultante en la oblea suele ser cuatro veces más pequeña, linealmente, que el patrón de la máscara.
Más exposición
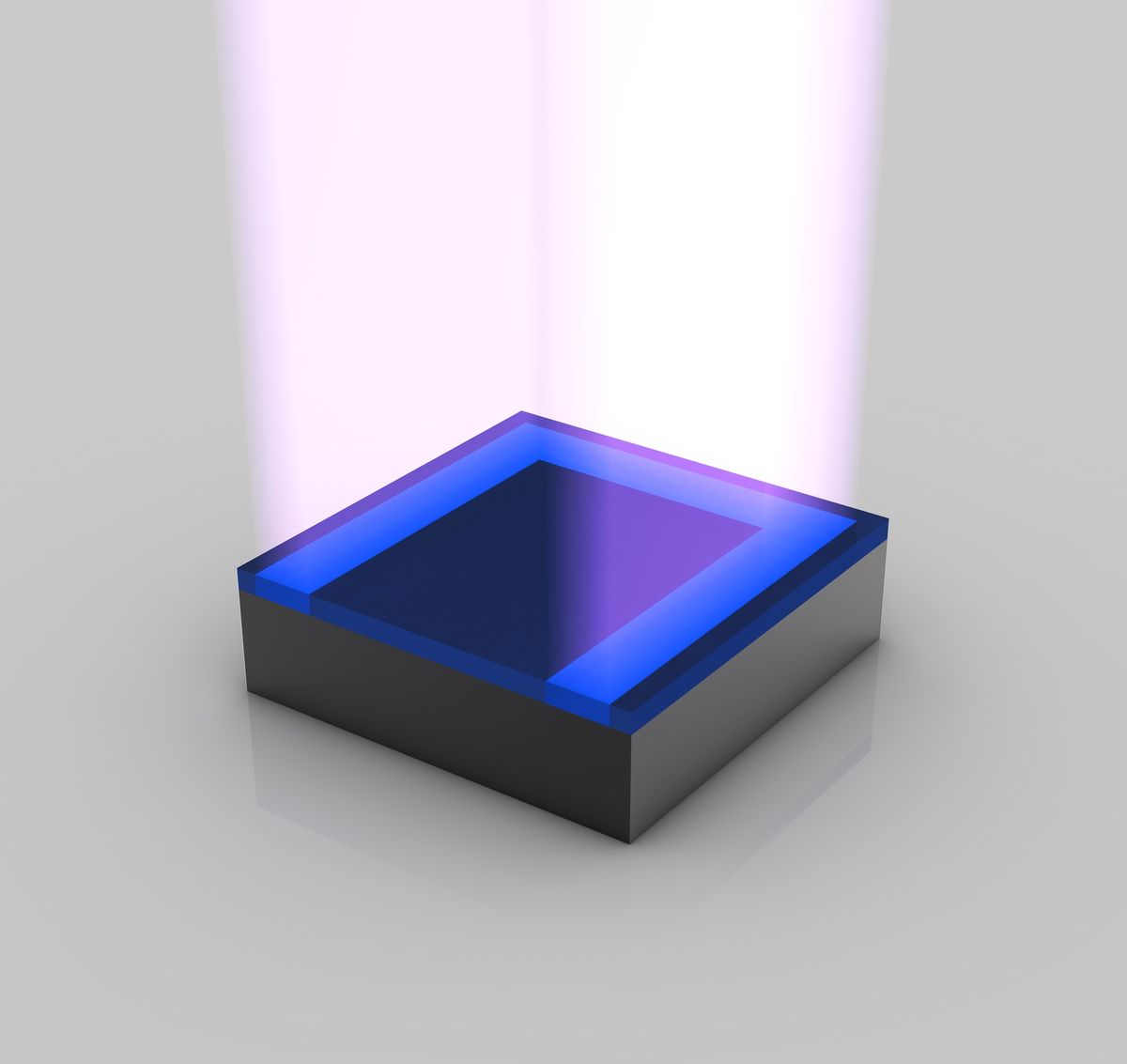
En la imagen tenemos una representación de cómo sería un único transistor si pudiéramos verlo a simple vista. Un transistor actúa como un interruptor, controlando el flujo de la corriente eléctrica en un chip de ordenador. Los investigadores de Intel han desarrollado transistores tan pequeños que afirman que unos 30 millones de ellos podrían caber en la cabeza de un alfiler.
Lavado de fotorresistencia
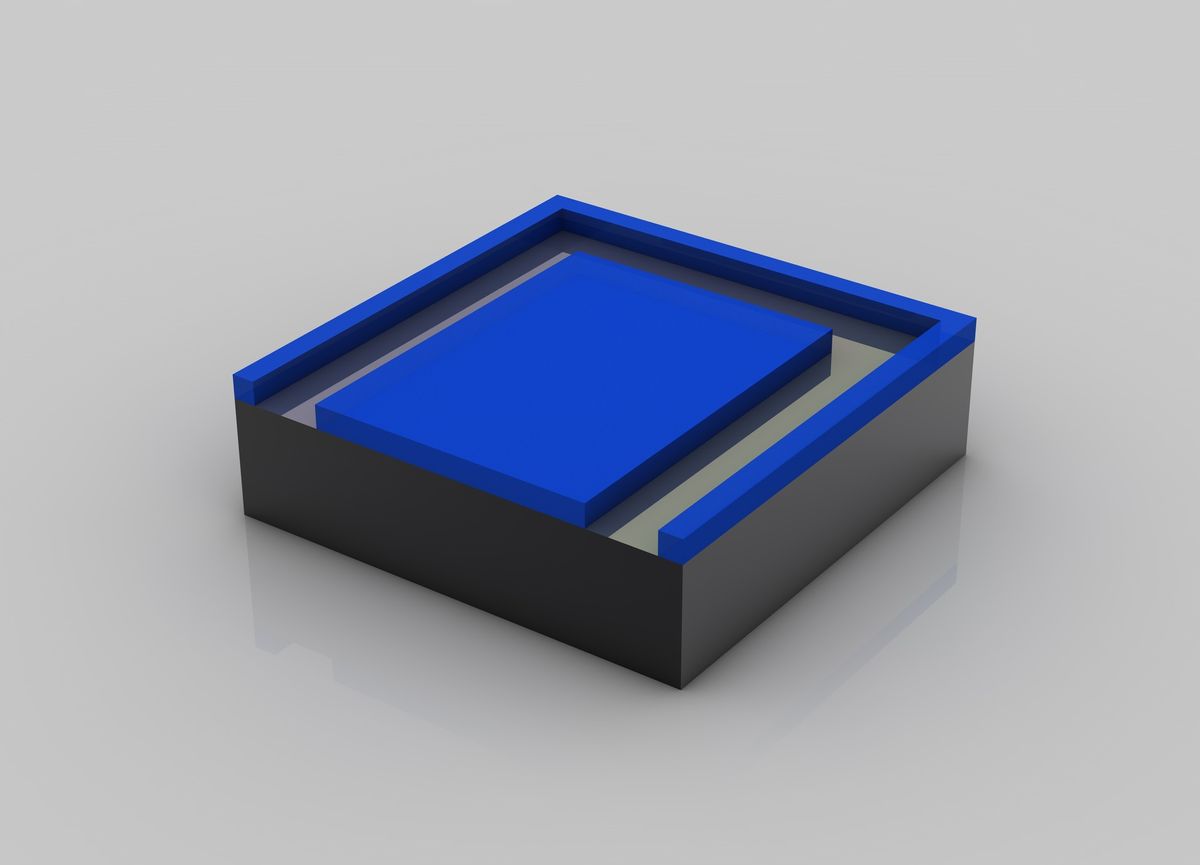
Después de ser expuestas a la luz ultravioleta, las zonas de fotorresistencia azul expuestas se disuelven completamente con un disolvente. Esto revela un patrón de fotorresistencia hecho por la máscara. A partir de este punto comienzan a crecer los transistores, las interconexiones y otros contactos eléctricos.
Grabado
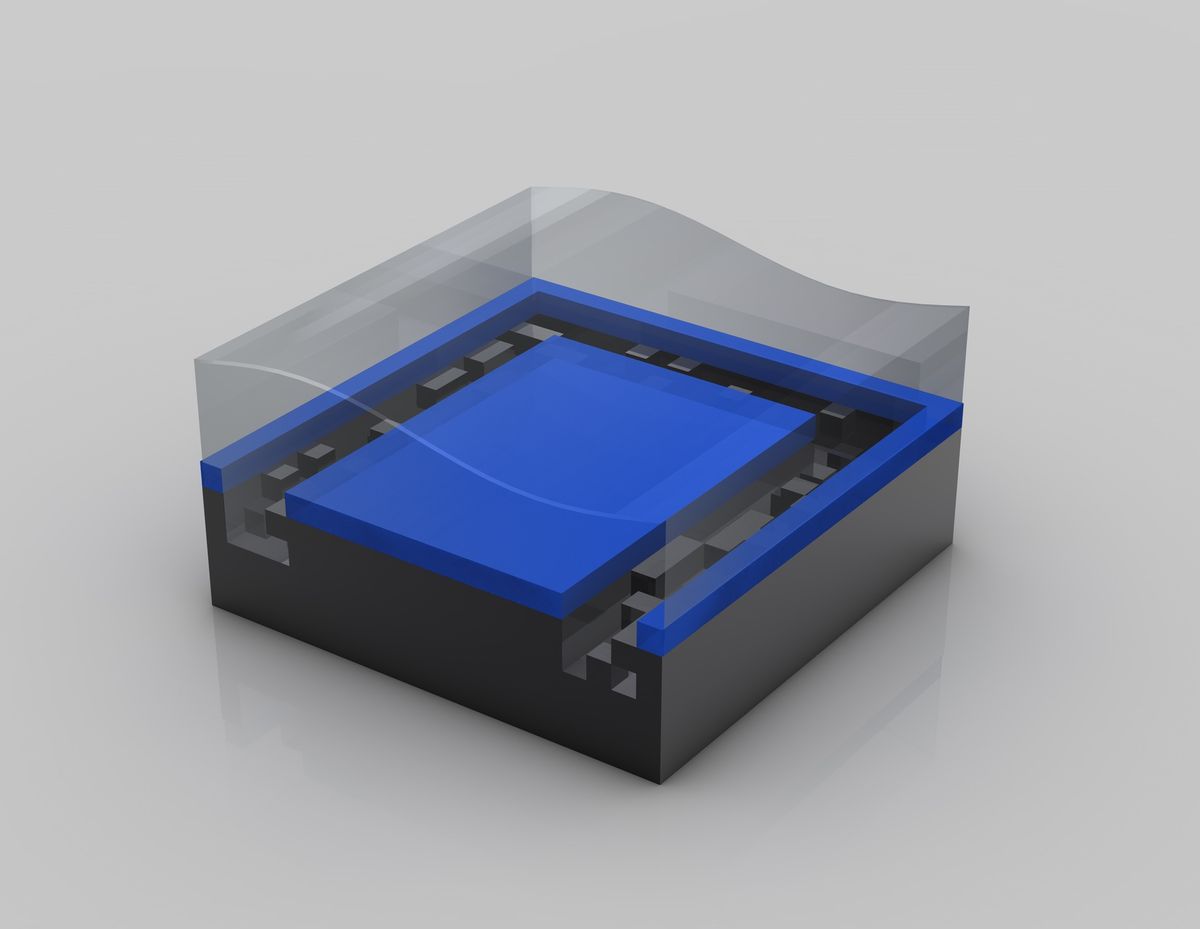
La capa de fotorresistencia protege el material de la oblea que no debe ser grabado. Las áreas que quedaron expuestas se eliminarán con productos químicos.
Retirada de la fotoresistencia
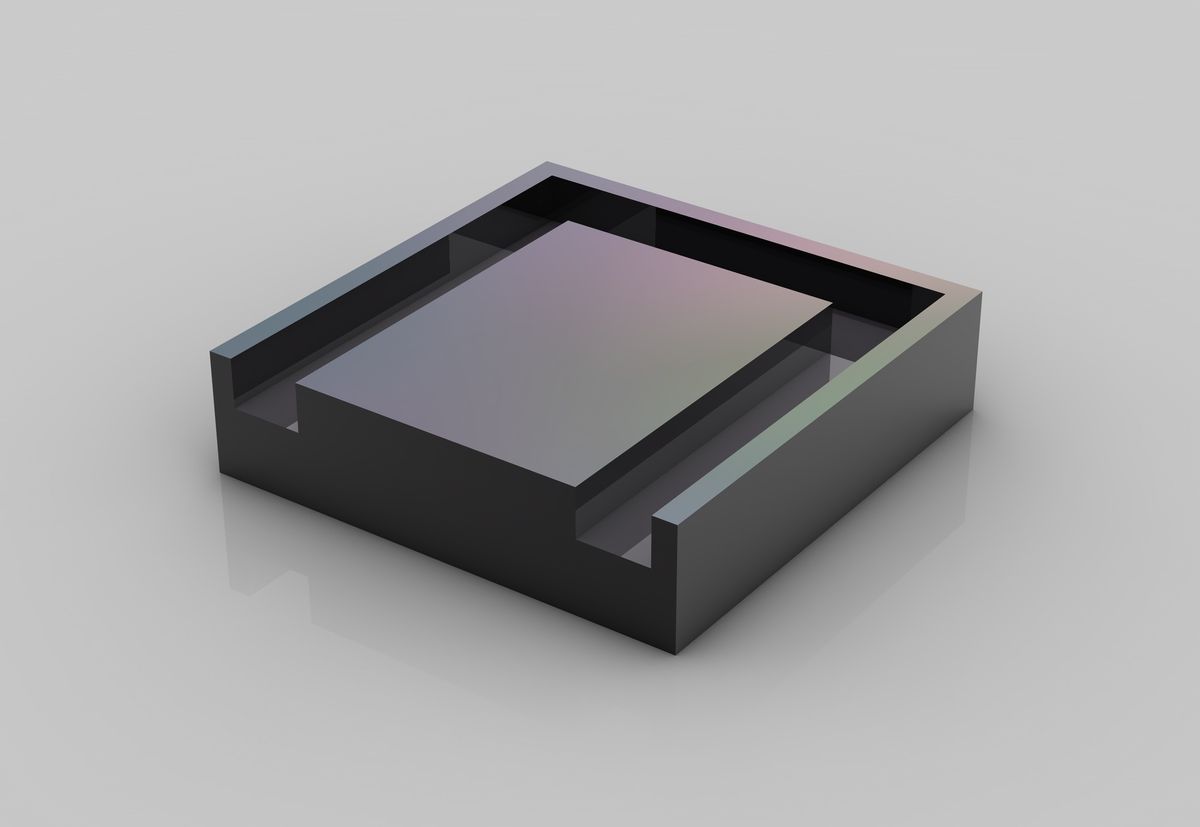
Después del grabado, se retira la fotoresistencia y se hace visible la forma deseada.
Noticias recientes